Nonwoven fabrics are a category of textiles that do not require weaving processes. These fabrics are made from short (staple) or long (continuous) fibers that are bonded together using chemical, mechanical, thermal, or solvent methods. The discovery and development of nonwoven fabrics began in the 1940s and 1950s, when there was a need for cheaper and lighter materials in various industries, including medical and packaging. Consequently, the production of these fabrics increased.
Applications of Nonwoven Fabrics
- Medical and Healthcare Industries
- Automotive and Transportation Industries
- Packaging and Filtration Industries
- Textile and Apparel Industries
Medical and Healthcare Industries
Nonwoven fabrics are widely used in the medical and healthcare sectors due to their high absorbency, softness, and resistance to liquids and bacteria. Nonwoven fabrics are utilized in the production of baby diapers, feminine hygiene products, surgical masks, hospital gowns, and wet wipes.
Baby Diapers and Feminine Hygiene Products: Nonwoven fabrics are used in the production of baby diapers, sanitary pads, and tampons. These fabrics are suitable for these hygiene products due to their high absorbency and softness on the skin.
Masks and Medical Apparel: Nonwoven fabrics are used in the manufacture of surgical masks, hospital gowns, and protective covers. These fabrics help maintain hygiene and safety due to their resistance to liquid and bacterial penetration.
Wet Wipes and Cleaners: Nonwoven fabrics are employed in the production of wet wipes and cleaners. These wipes are suitable for cleaning and disinfecting due to their high absorbency and softness.
Automotive and Transportation Industries
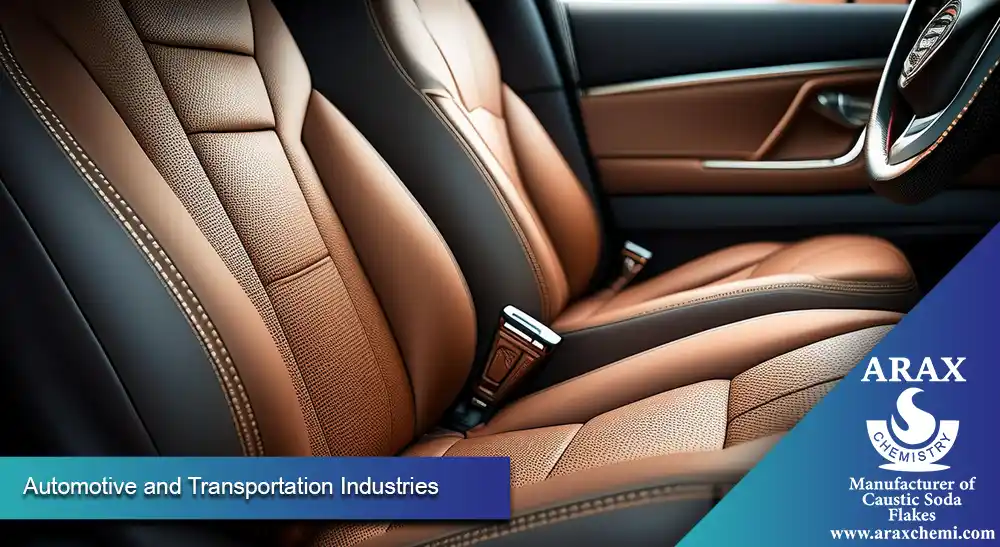
Nonwoven fabrics are used in automotive applications for soundproofing and thermal insulation due to their light weight and high performance in sound absorption and temperature retention. They are also used in interior upholstery to enhance comfort and appearance.
Soundproofing and Insulation: Nonwoven fabrics are utilized in automotive soundproofing and thermal insulation. Due to their light weight and efficiency in absorbing sound and maintaining temperature, these fabrics are suitable for insulating various parts of vehicles.
Interior Upholstery: In vehicle interior upholstery, nonwoven fabrics are used as underlayers and soft coverings. Their softness and high resistance contribute to the improvement of vehicle interior comfort and aesthetics.
Packaging and Filtration Industries
Nonwoven fabrics are employed in packaging for protective purposes due to their resistance to impact and moisture. They are also used in filters for air, water, and oil due to their high efficiency in capturing particles and impurities.
Protective Packaging: Nonwoven fabrics are used in protective packaging due to their resistance to impact and moisture. They are suitable for packaging sensitive and fragile products.
Industrial and Household Filters: Nonwoven fabric is used in the production of air, water, and oil filters. Their efficiency in capturing particles and impurities makes them suitable for industrial and household filtration applications.
Textile and Apparel Industries
Nonwoven fabrics are used in the production of disposable garments such as hospital gowns due to their light weight and resistance to liquid penetration. They are also used in technical and sportswear as insulating and protective layers due to their light weight, softness, and breathability.
Disposable Garments: Nonwoven fabric is used in the production of disposable garments such as hospital gowns and protective clothing. Their lightweightness and resistance to liquid penetration make them suitable for use in healthcare and industrial environments.
Technical and Sportswear: In technical and sportswear, nonwoven fabrics are used as insulating and protective layers. Their lightweightness, softness, and breathability make them ideal for garments designed for athletic activities and harsh environments.
Manufacturing of Nonwoven Fabrics
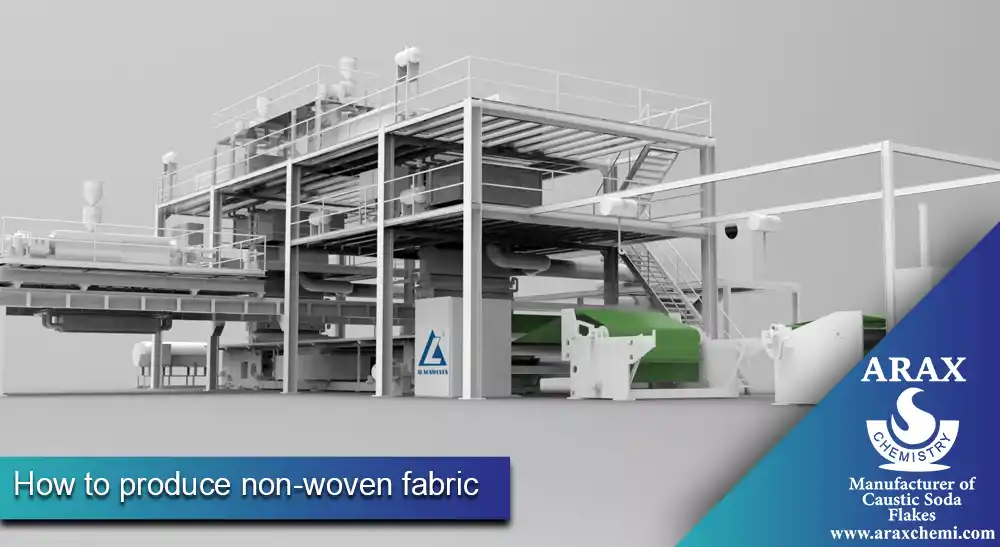
The production of nonwoven fabrics involves converting fibers into fabric without weaving. This process is achieved through mechanical (needling or water jets), chemical (using adhesives and chemicals), and thermal (using heat and pressure) methods. Nonwoven fabric is used in various industries including medical, automotive, packaging, and textiles.
Mechanical Methods
Needle Punching: In this method, fibers are compressed together using specialized needles to produce a strong and durable fabric. These fabrics are typically used for industrial applications and filtration.
Spunlace: In this method, fibers are compressed together using high-pressure water jets to produce a soft and flexible fabric. These fabrics are suitable for making wet wipes and hygiene products due to their softness and high absorbency.
Chemical Methods
Chemical Bonding: In this method, fibers are bonded together using adhesives and chemicals. This method is suitable for producing water- and chemical-resistant fabrics.
Foam Bonding: In this method, fibers are bonded together using foams and chemicals to produce a strong and durable fabric. These fabrics are suitable for industrial and construction applications.
Thermal Methods
Thermal Bonding: In this method, fibers are bonded together using heat. This method is suitable for producing lightweight and durable fabrics. Fabrics produced using this method are typically used in hygiene products and filters.
Calendaring: In this method, fibers are compressed together using pressure and heat to produce a soft and flexible fabric. These fabrics are used for making disposable garments and hygiene products.
Post-Production Processes
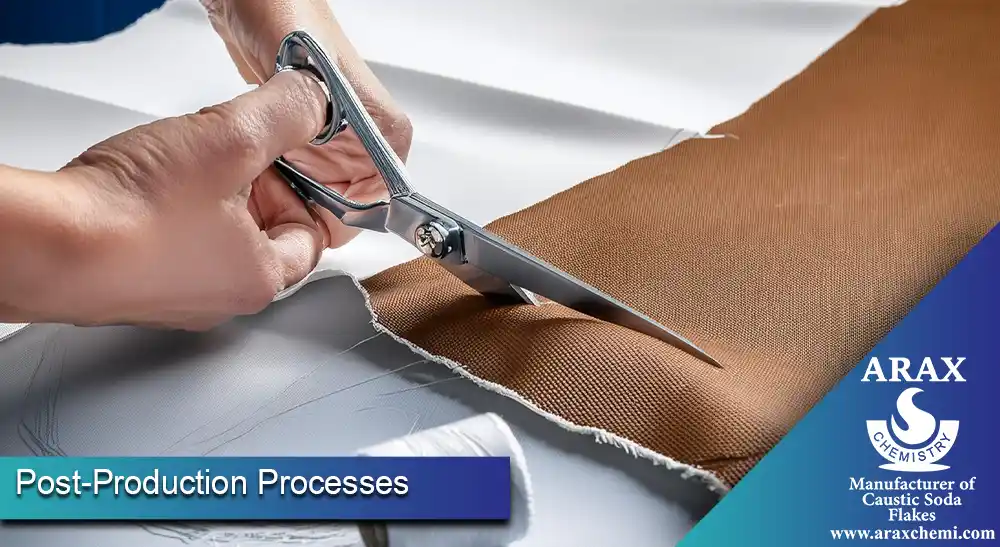
Cutting and Sewing
After production, nonwoven fabric is cut and sewn into various sizes and shapes. This is done using advanced technologies such as laser cutting and CNC machines, which offer high precision and speed. CNC cutting allows for complex shapes to be created, and laser cutting seals the edges to enhance fabric strength.
Sewing is performed with industrial machines and ultrasonic technology, which uses sound waves to bond fibers, reducing the need for sewing threads. These methods are particularly suitable for producing high-strength and leak-proof medical and hygiene products.
Waterproofing and Packaging
After cutting and sewing, nonwoven fabrics are treated with polymer coatings or heat treatments to improve their water resistance and chemical resistance. These processes may include laminating or applying nano-coatings.
Conclusion
Nonwoven fabrics have extensive applications across various industries due to their unique properties such as light weight, softness, resistance to liquid penetration, and high absorbency. These fabrics are produced using different manufacturing methods, each offering distinct properties suited to specific industrial needs. With the continuous advancement of nonwoven fabric technologies, their applications are expected to expand further in the future.
F A Qs
- Which people are nonwoven fabrics suitable for?
Nonwoven fabrics are suitable for individuals who need products with high absorbency and softness, such as patients, children, and those requiring medical and hygiene products. They are also suitable for manufacturers seeking lightweight and durable materials for industrial and packaging applications. - Are nonwoven fabrics more widely used than woven fabrics?
Both types of fabrics have their own specific applications. Nonwoven fabrics are more commonly used in the medical, hygiene, and packaging industries, while woven fabrics are primarily used in clothing, furniture, and interior decoration. Overall, nonwoven fabric has broader applications in sectors requiring high absorbency and resistance to liquid penetration. - Which fabric is stronger?
Woven fabrics generally have greater strength due to their more organized and robust fiber structure. However, nonwoven fabrics can also achieve suitable strength for various applications, especially where light weight and flexibility are needed.