Aluminum is a valuable and lightweight metal used in various industries, including aerospace, automotive, packaging, and construction. Extracting aluminum from bauxite ore, which contains aluminum, requires complex chemical processes. One of the crucial chemicals in this process is caustic soda (NaOH), which is extensively used in the extraction and purification of aluminum.
History of Aluminum Extraction
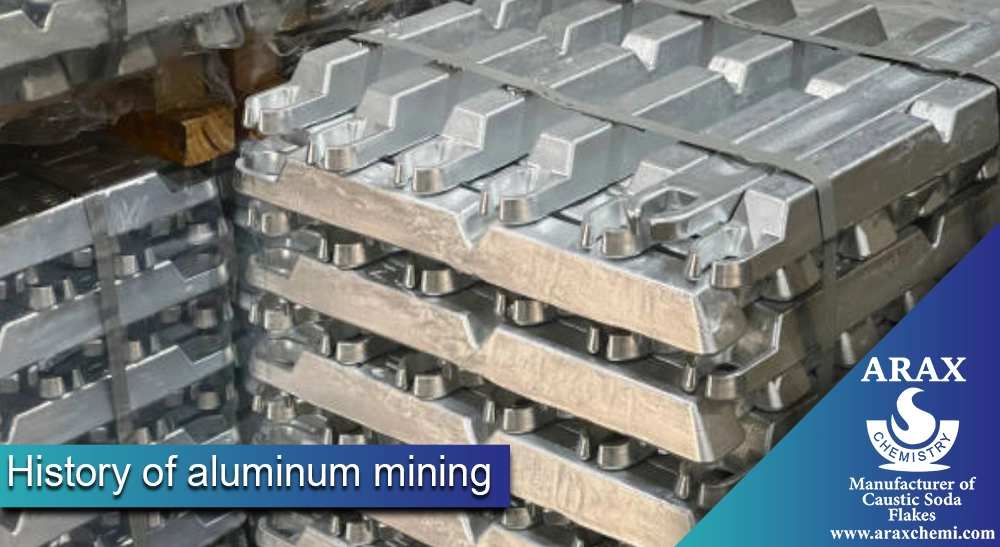
The first industrial aluminum extraction process was developed by Charles Martin Hall and Paul Héroult in 1886, known as the Hall-Héroult process. This process involves the electrolysis of aluminum oxide (Al2O3) in molten cryolite (Na3AlF6). However, before this stage, bauxite ore must be converted into pure aluminum oxide through the Bayer Process.
The Bayer Process and the Role of Caustic Soda
The Bayer Process is an industrial method used to extract alumina (aluminum oxide) from bauxite ore. Alumina is the primary raw material for aluminum production. This process was developed by Karl Joseph Bayer in the late 19th century. Here are the main steps of the Bayer Process in detail:
Crushing and Grinding of Bauxite
– Bauxite ore is extracted from the mine and transported to the plant. In the first step, the bauxite is crushed into smaller pieces to increase its surface area for the caustic soda solution. The crushed bauxite is then ground into a powder.
Dissolution of Bauxite in Caustic Soda Solution
The bauxite powder is mixed with a caustic soda solution at high temperatures (150 to 200°C) and high pressure (4 to 7 bar) in autoclave reactors. In this step, caustic soda reacts with the aluminum in the bauxite to form sodium aluminate (NaAlO2). The primary chemical reaction is as follows:
3Al(OH)3+NaOH→Na[Al(OH)4
Clarification
The resulting solution from digestion contains dissolved sodium aluminate and undissolved solid residues (known as red mud). This mixture is transferred to settling tanks. The mixture separates into solid phases (bauxite residue) and liquid (sodium aluminate solution). Filtration separates the solid from the liquid.
Precipitation
The clarified sodium aluminate solution is transferred to precipitation tanks. Here, by lowering the temperature and using aluminum hydroxide seed crystals, dissolved alumina precipitates as aluminum hydroxide (Al(OH)3):
Na[Al(OH)4]→3Al(OH)3+NaOH
Filtration and Washing
The precipitated aluminum hydroxide is separated from the solution and washed to remove any remaining caustic soda.
Calcination
The aluminum hydroxide is transferred to calcination kilns and heated at about 1000 to 1100°C to remove water and produce pure alumina:
2Al(OH)3→Al2O3+3H2O
Caustic Soda Recovery

The caustic soda solution remaining from the clarification step is recovered and returned to the beginning of the process for reuse.
Quality Control
The produced alumina must be controlled and inspected to ensure it meets the quality requirements for aluminum production. This process is highly efficient and allows for the recycling of chemical materials, making it one of the most important industrial methods for producing alumina.
benefits of Using Caustic Soda in the Bayer Process

The use of caustic soda (sodium hydroxide, NaOH) in the Bayer process for extracting alumina from bauxite offers several key advantages. Here are the benefits in detail:
- Increased Efficiency in Alumina Extraction
Caustic soda, due to its strong alkaline nature, effectively extracts alumina from bauxite. It reacts with the aluminum oxide in bauxite to form sodium aluminate (NaAlO2), which dissolves easily in water and separates from other bauxite compounds. - Formation of Sodium Aluminate Solution
Sodium hydroxide reacts with alumina to form a sodium aluminate solution. This solution is easily separable from other minerals and impurities in bauxite, facilitating the alumina extraction process. - Recycling and Reusing
One of the significant advantages of using caustic soda in the Bayer process is its ability to be recycled and reused after various stages of the process. This feature reduces operational costs and the need for new chemical materials. - Process Stability and Control
– Sodium hydroxide is easily controllable and adjustable. This allows process engineers to precisely control and optimize operating conditions to maximize alumina extraction from bauxite. - Fast Reaction Rate
Caustic soda reacts quickly with alumina, increasing the overall speed of the extraction process. This feature allows plants to produce alumina in a shorter time, enhancing process efficiency. - Energy Consumption Reduction
Using caustic soda at lower temperatures compared to other similar chemical methods is possible. This reduces energy consumption in the Bayer process, leading to lower energy costs. - Compatibility with Industrial Equipment
Sodium hydroxide is compatible with many structural materials used in industrial equipment. This increases equipment lifespan and reduces maintenance and repair costs. - Safety and Easy Management
Sodium hydroxide is a chemical that, with proper safety measures, is relatively simple and safe to manage and use in the industry. Numerous methods for safe transportation, storage, and use of this chemical exist, ensuring industrial safety.
Challenges and Environmental Issues
Despite its many advantages, the use of caustic soda in aluminum extraction poses specific challenges and environmental issues:
Solid Waste Management
After bauxite dissolution, the remaining solids contain alkaline compounds and heavy metals, potentially harming the environment. Proper and safe management of these wastes is essential.
Water Consumption
The Bayer process requires large amounts of water, potentially stressing local water resources.
Greenhouse Gas Emissions
Heating aluminum hydroxide to produce aluminum oxide requires significant energy, usually derived from fossil fuels, leading to greenhouse gas emissions.
Innovations and the Future of Aluminum Extraction
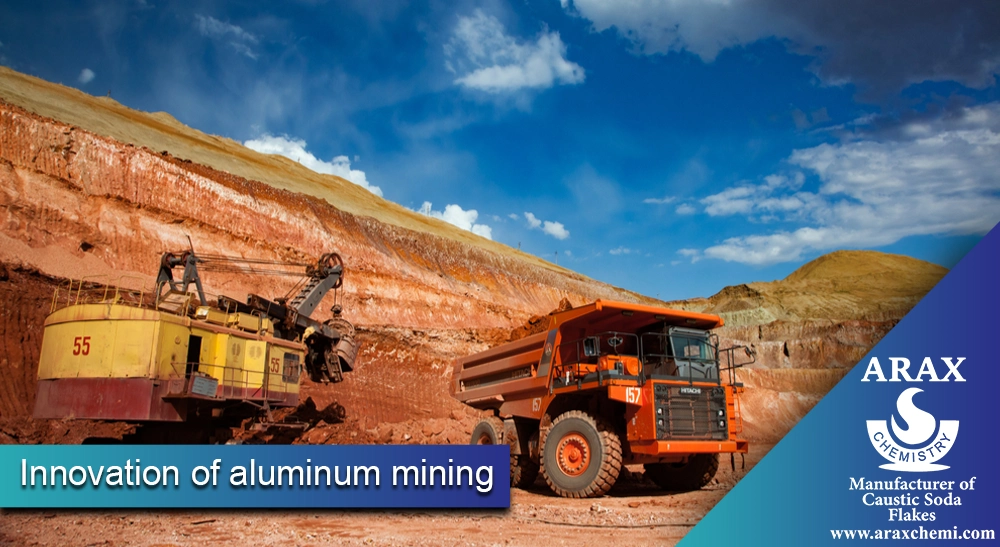
Given the increasing importance of environmental issues and the need to improve aluminum production efficiency, research and innovation in this field continue. Some expected future advancements include:
New Technologies in the Bayer Process
Developing more efficient methods for bauxite dissolution and reducing caustic soda consumption can increase efficiency and lower production costs. Innovations such as using alternative chemicals with higher efficiency and less environmental impact, improving mechanical and chemical processes, and optimizing reaction conditions can be effective. Implementing these technologies reduces caustic soda consumption and operational costs, increasing alumina extraction from bauxite.
Recycling Solid Wastes
Research and development of technologies for recycling and reusing bauxite residues and other wastes generated in the Bayer process can help reduce environmental impacts. These wastes often contain compounds that can be reused in industrial processes. Advanced technologies such as chemical and physical separation, converting wastes into valuable materials, and developing environmentally friendly methods for disposing of harmful substances can improve waste management and reduce environmental pollution.
Energy Consumption Reduction
Using renewable energy sources and optimizing thermal and electrolysis processes can help reduce energy consumption and greenhouse gas emissions. Technologies such as solar panels, wind turbines, and fuel cells can reduce reliance on fossil fuels. Additionally, improving the efficiency of calcination kilns and electrolysis, and using high-efficiency materials for insulation and reducing heat loss can save energy and lower production costs.
Improving Aluminum Quality
Using advanced technologies and more precise process control can improve the quality of produced aluminum, making it more suitable for sensitive applications such as aerospace and electronics industries. This includes optimizing chemical composition, reducing impurities, and enhancing aluminum’s mechanical and physical properties. Precise reaction condition control, using high-purity raw materials, and employing advanced equipment to produce high-quality aluminum are some measures that can improve the final product quality.
Conclusion
Caustic soda plays a crucial role in the extraction and purification of aluminum, significantly enhancing the efficiency of bauxite dissolution and reducing production costs, making aluminum extraction more economical. However, challenges associated with caustic soda usage require careful attention and management.
With technological advancements and new innovations, there is hope for a more sustainable and efficient aluminum extraction process. These advancements will not only help preserve the environment but also enhance the competitiveness of the aluminum production industry in the global market. Consequently, a combination of optimal resource management, the use of new technologies, and attention to environmental issues can lead to the sustainable development of this vital industry.
Frequently Asked Questions
- How is the aluminum extraction process done with caustic soda?
First, bauxite, which is the raw material containing aluminum, is crushed and mixed with caustic soda. This mixture is placed in a reactor under pressure and temperature to separate the soluble sodium aluminate and other insoluble materials. Then, the aluminate solution is cooled and separated, and by adding aluminum hydroxide to the solution, alumina (aluminum oxide) is obtained, which turns into metallic aluminum after heating. - Why is caustic soda used in aluminum extraction process?
Caustic soda is used due to its strong alkalinity and ability to dissolve aluminum from its mineral compounds, especially bauxite. This substance can convert aluminum into soluble sodium aluminate, which enables the separation and purification of aluminum. - What are the benefits of using caustic soda in aluminum extraction?
• High efficiency in extracting aluminum from bauxite
• Lower cost than other methods
• A fast and efficient process
• Ability to recycle caustic soda for reuse in the process